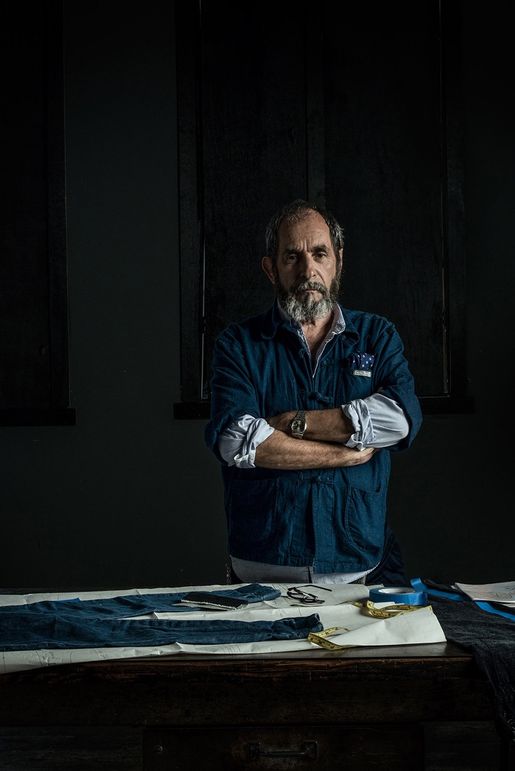
Why should we care about denim going green? Because this is the foundation of streetwear and youth culture fashion.
First, during Texworld in Paris from February 15-19, 2016, according to Sportswear International, François Girbaud and Pakistani denim mill Naveena Denim Ltd (NDL) announced their new collaboration.
Girbaud was once the brand of the 80’s and early ‘90’s. The denim that all college trendsetter wore then, proudly sporting the white tag label on the zipper. According to Girbaud who is still in the process of a comeback, “Denim was dead in the ’70s. When we started with stone wash, sanforization and chemical treatments we only wanted one thing: to make denim big! But we had not considered that this would have been extremely harmful for the environment and for generations to come.”
On his past: “I made a big mistake! I helped to destroy the planet! But we didn’t know any better back then. Today, we do.” Apparently since 1989, Girbaud has been testing sustainability.
According to Sportswear International, “Referring to ozone treatments, a finishing technique already practiced in Pakistan long before than in Europe,” Girbaud commented: “I cannot turn back the time but I want to dedicate my last active years to make the best of a bad job and with NDL Naveena I have found the perfect partner.”
NDL is also working with Levi Strauss. “The future is in our hands”, commented Masood Riaz, NDL’s owner and president. “We must invest in the future by educating our staff, by acquiring the best equipment, and by making an effective contribution to sustainable technologies and productive methods.”
Rashid Iqbal, executive director, NDL, also commented on the collaboration with Girbaud: “We share one vision,” he commented. “Together with François Girbaud we will re-invent denim and develop the most prestigious water, chemical free technologies and state-of-the-art fabrics to help save the planet.”
Bionic Yarn and Fashion Positive Get Cradle to Cradle Certification
Raw Material Engineering company Bionic, creator of Bionic Yarn (Pharrell William’s collab), in partnership with Fashion Positive, has recently been awarded a Cradle to Cradle certification at the BRONZE-Level for its HLX and DPX yarn structures. The unique and refined texture of HLX yarns and the versatility of DPX yarns enable product designers and brands to achieve environmental impact, performance, and quality in both industrial and consumer applications.
From its inception, Bionic has been a company founded on creating the most durable of textiles made from recycled plastic with the ultimate goal of helping the environment. They knew that achieving a Cradle to Cradle certification was paramount to that goal.
“We pride ourselves on the environmental impact and accomplishments Bionic has achieved over the years, however when William McDonough challenged us to push our vision to the limit, we knew it was time to take it to the next level.”
Here’s more:
HLX is a patented yarn made with recycled plastic and designed to deliver durability. The helix structure provides texture while wrapping an RPET core. Fibers for the helix and core of the yarn are selected to precisely match functional and aesthetic requirements. HLX is suitable for high-performance applications including outerwear, automotive, commercial and industrial uses.
DPX is offered in two composition options: a dual staple fiber construction that blends recycled PET fibers together with natural fibers to form a yarn with a soft texture; and a recycled PET yarn (100% RPET). DPX is suitable for both knit and woven fabric applications and is available in ring, siro, open-end, air-jet and vortex spun forms.
A key component of the Cradle to Cradle Certified Product Registry , BIONIC HLX and DPX are the only yarns containing recycled plastic that have been certified by the Cradle to Cradle Products Innovation Institute.
HLX and DPX yarns are Cradle to Cradle Certified BRONZE-Level, and have shown achievements in the following areas:
• At least 75% of materials by weight have been assessed.
• The product’s homogeneous materials do not contain banned list chemicals above permitted thresholds.
• Products/materials are designed to be recycled or to biodegrade and a pilot project focused on recycling the yarns is on-going.
• Facility wide water audit has been completed.
• A renewable energy use and carbon management strategy has been developed.
• A full social responsibility self-audit has been completed and a positive impact strategy has been developed, if needed.